Anyone who works in aerospace understands that quality in manufacturing is non-negotiable. To ensure that parts meet quality requirements and function safely under extreme conditions, manufacturers must adhere to specific standards.
Read More
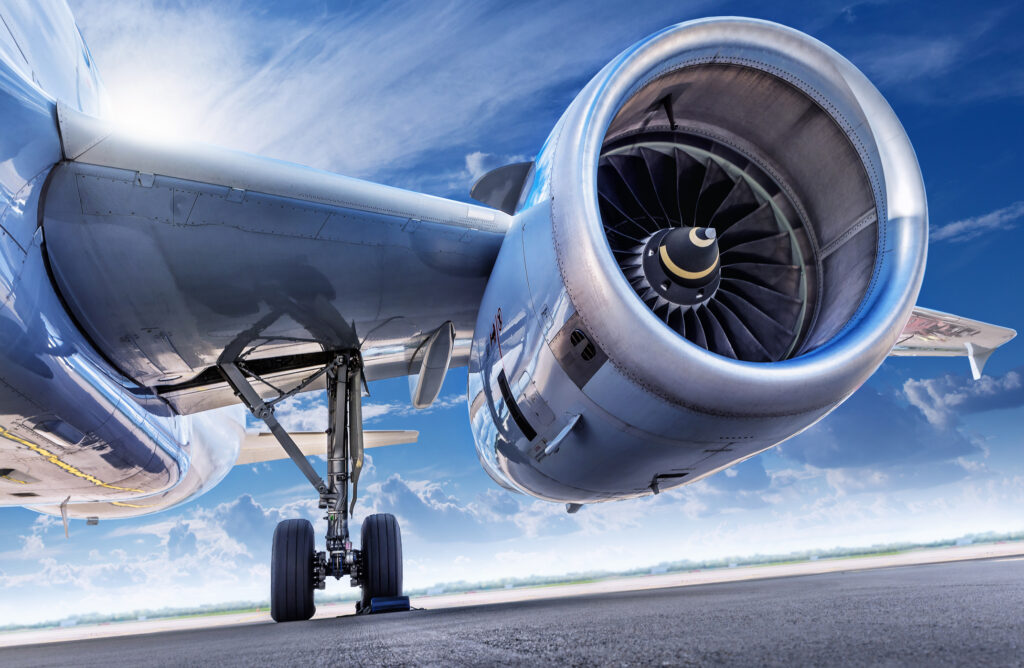